Plant & Process
4.O INDUSTRIAL Ai
The Problem
Modern mining plants face a host of challenges that hinder efficiency and productivity. One of the key problems is fragmented data across various systems, including equipment sensors, process control systems, and environmental monitoring platforms. These disparate data sources create silos that make it difficult for engineers to get a comprehensive, real-time view of operations. This fragmentation leads to inefficiencies in decision-making, as engineers and operators cannot easily access or analyze the full scope of plant data, resulting in delayed responses to process deviations, equipment failures, or environmental concerns.
Another major issue is inconsistent process control. Variability in ore quality, equipment performance, and environmental conditions means that mining processes need to be constantly adjusted. Without integrated data and advanced process control systems, these adjustments are often reactive, leading to suboptimal recovery rates, energy inefficiency, and higher operational costs. Equipment downtime, driven by both unplanned maintenance and inefficient resource management, further exacerbates these issues. The inability to predict failures or optimize maintenance schedules results in production delays, lost revenue, and increased maintenance costs.
On top of these operational challenges, modern mining plants must adhere to strict environmental and safety regulations. Managing the environmental impact—from tailings management to water and air quality control—requires advanced monitoring systems that are often disconnected from the core production systems. This increases the complexity of compliance reporting and limits the ability to proactively address potential violations.
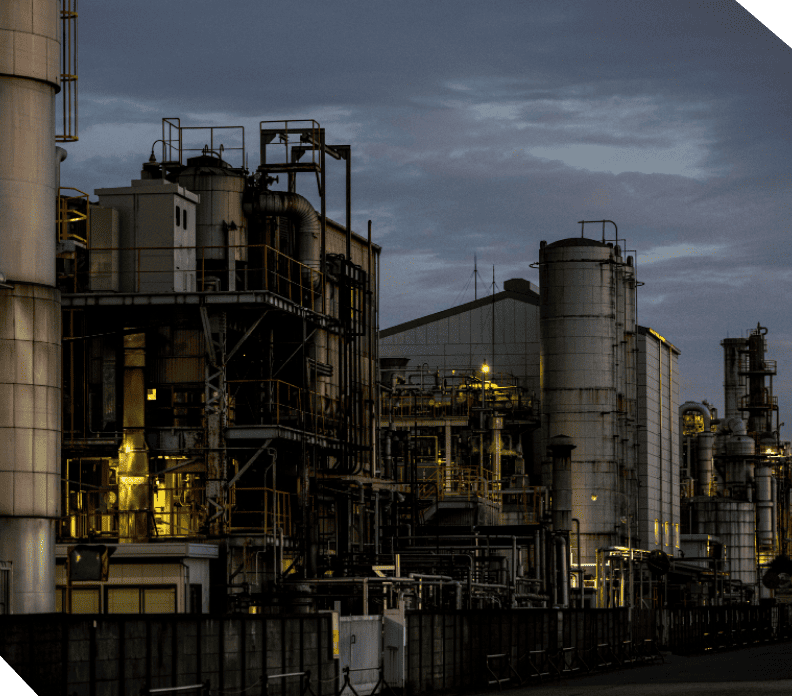
4.O INDUSTRIAL Ai
The Solution
Our Digital Twin solution addresses the critical challenges faced by modern mining plants by unifying disparate data across OT, IT, and environmental systems into a single, real-time view. This integration enables improved decision-making, more efficient resource management, and dynamic process control that adjusts to changing conditions, optimizing recovery rates and reducing downtime.
With built-in predictive maintenance tools, the solution helps minimize unplanned equipment failures, ensuring optimal performance and extending the lifecycle of critical machinery. Additionally, it provides seamless integration of environmental monitoring systems, enabling real-time compliance tracking for stringent safety and environmental regulations.
To safeguard operations, our platform delivers out-of-the-box PROTECTED level cybersecurity, ensuring robust protection for both OT and IT systems while meeting regulatory requirements. This comprehensive approach secures critical infrastructure, streamlines compliance, and reduces operational risks, empowering engineers to manage complex processes with greater efficiency and confidence in today’s highly regulated mining environment.
REQUEST A DEMO
Let’s Talk
Have some questions that weren’t answered on the website, let us know.